Exploring the Six Sigma Quality Management System
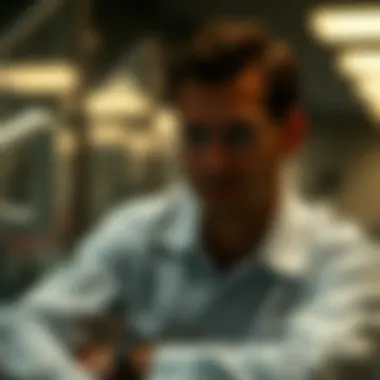
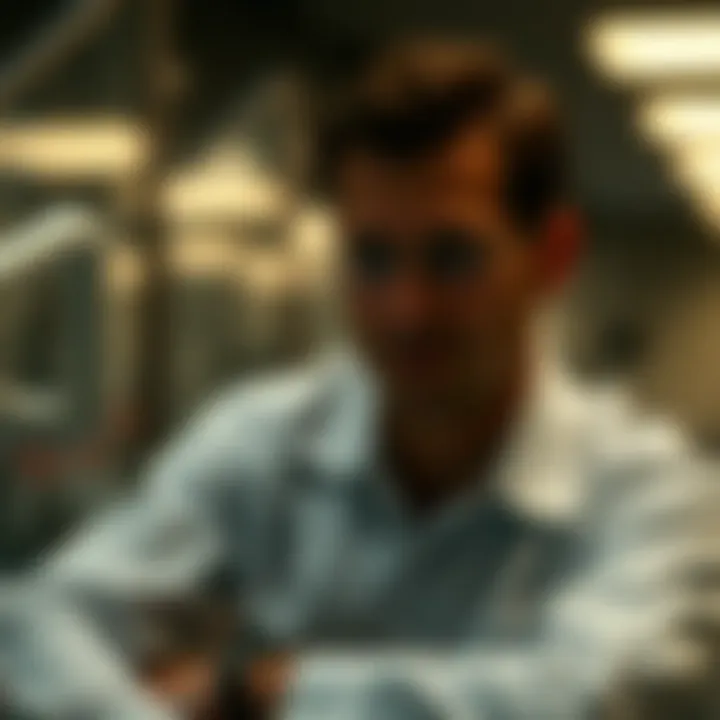
Intro
In the ever-evolving landscape of business management, the Six Sigma quality management system stands out as a beacon for operational excellence. Designed to enhance organizational efficiency and effectiveness, it's a structured approach that is not just about quality management, but it's also deeply intertwined with business strategy. Its core methodologies are centered around reducing variation and eliminating waste, leading to substantial improvements in processes across varying industries.
Understanding Six Sigma means delving into its rich history, exploring how it originated, and comprehending its evolution over time. The principles of Six Sigma, rooted in statistical analysis, have gone on to blanket numerous sectors, from manufacturing to healthcare, adapting to the unique challenges faced by each. As we embark on this comprehensive examination, it’s crucial to grasp the significance of its methodologies - chiefly the DMAIC and DMADV frameworks.
Moreover, this article catches a glimpse of the various Six Sigma belts, the custodians of these methodologies, who play vital roles in implementing these strategies effectively. As we string together these insights, it becomes apparent that understanding Six Sigma is not a luxury but a necessity for anyone invested in optimizing performance and maximizing results in their field of work.
Understanding Six Sigma
Understanding Six Sigma is paramount to grasping its transformative impact on various sectors, particularly in today’s fast-paced business environment. The essence of Six Sigma lies not just in its unique methods but also in its philosophy of relentless pursuit of quality and efficiency. A clear understanding of this management framework equips businesses with tools and processes that can significantly reduce waste, optimize performance, and improve customer satisfaction.
By folding the principles of Six Sigma into organizational DNA, firms can create a culture that prioritizes data-driven decision-making and aligns operational practices with strategic goals. This intrinsic knowledge allows practitioners and stakeholders to breed innovation while systematically addressing issues that inhibit success. Six Sigma isn’t merely about numbers; it’s about cultivating a mindset that welcomes change and adapts swiftly to market demands.
Definition and Principles
Six Sigma is defined as a set of techniques and tools for process improvement. It utilizes a data-driven methodology to identify and eliminate defects in any process—from manufacturing to transactional and from product development to service. At its core, Six Sigma operates on the principle that if you can measure how many defects you have in a process, you can systematically figure out how to eliminate them and get as close to zero defects as possible.
The principles of Six Sigma are often encapsulated in the acronym "DMAIC," which stands for Define, Measure, Analyze, Improve, and Control. Each of these stages plays a critical role in improving processes:
- Define: Identify the problem and the project goals.
- Measure: Collect data and determine the current performance level.
- Analyze: Examine the data to discover root causes of defects.
- Improve: Implement solutions to eliminate the root causes.
- Control: Monitor the improvements to sustain gains over time.
Historical Context
The roots of Six Sigma can be traced back to the 1980s at Motorola, where the concept was developed as a response to increased global competition and a growing demand for better product quality. Japanese manufacturers were setting a high bar with their processes, and it became clear that American companies needed to adapt or risk obsolescence. During the 1990s, Six Sigma gained traction when General Electric adopted it under Jack Welch, positioning it as a central tenet of its operational strategy. This meant embracing data and methodology as a way to secure victories in quality and customer satisfaction.
As industries began to recognize the power of Six Sigma, it expanded beyond manufacturing into other fields, including services, healthcare, and finance. This evolution reflects a growing understanding that the principles can be universally applied to yield better business outcomes.
Importance in Quality Management
The importance of Six Sigma in quality management cannot be overstated. It serves as a backbone for organizations aiming to enhance their operational processes and deliver superior products or services. The primary benefits include:
- Increased Customer Satisfaction: By focusing on quality and reducing defects, companies can better meet customer expectations, fostering loyalty.
- Cost Reduction: Streamlining processes minimizes waste and inefficiency, which in turn leads to significant cost savings.
- Enhanced Employee Engagement: Six Sigma encourages a culture of continuous improvement, motivating employees to contribute to enhancements and take ownership of their work.
- Data-Driven Decisions: This quality management system deploys objective metrics, ensuring choices are based on solid evidence rather than gut feelings.
"Quality is more than just an aim; it’s a continuous journey towards perfection."
In summary, an in-depth understanding of Six Sigma lays the groundwork for effective quality management strategies. It fosters a systematic approach to problem-solving and creates an environment where quality can thrive.
Core Components of Six Sigma
Six Sigma stands as a beacon of excellence in quality management systems, and understanding its core components is crucial for any organization looking to boost efficiency and minimize defects. The foundation of Six Sigma is built on two main methodologies: DMAIC and DMADV, each serving a unique purpose in the realm of quality management. By grasping these core components, organizations can effectively streamline processes and reinforce their pursuit of operational perfection, thus positively impacting financial performance and customer satisfaction.
DMAIC Methodology
The DMAIC framework acts as a structured approach for improving existing processes by following five critical phases: Define, Measure, Analyze, Improve, and Control. This framework is particularly advantageous because it provides a clear roadmap for identifying process deficiencies and implementing solutions. Here's a brief look at each phase:
Define Phase
In the Define Phase, the primary objective is to outline the problem clearly. Organizations pinpoint what needs fixing and establish project goals. A key characteristic of this phase is the use of voice-of-the-customer (VOC) feedback, which ensures that improvements align with customer needs. This phase is beneficial because it sets the stage for everything that follows. One unique feature of the Define Phase is the project charter, which summarizes the scope, objectives, and team responsibilities. However, a disadvantage could be the time spent gathering detailed VOC data, which, although crucial, may delay the project kickoff.
Measure Phase
Next is the Measure Phase, where the focus shifts to quantifying the problem. Data collection is paramount, as organizations gather baseline metrics to understand current performance levels. The hallmark of this phase is the emphasis on statistical analysis, allowing organizations to identify key quality metrics. This approach is beneficial since it fosters evidence-based decision-making. A distinctive feature here is the development of a data collection plan that dictates what data should be gathered and why. On the flip side, the large volume of data can overwhelm a team if not managed properly, potentially skewing insights.
Analyze Phase
During the Analyze Phase, teams delve into the data to identify root causes of defects. The core characteristic of this phase is the structured problem-solving techniques used, such as fishbone diagrams and Pareto charts. This phase is beneficial because it helps teams see beyond surface symptoms to address underlying issues. The unique feature of the Analyze Phase is its capacity to reveal previously unseen process variations. A disadvantage, however, would be the possibility of misidentifying root causes if the analysis lacks thoroughness or if the wrong metrics are prioritized.
Improve Phase
Entering the Improve Phase, teams brainstorm solutions aimed at resolving identified root causes. This part of the process is characterized by creativity and practical experimentation, often involving pilot tests of proposed solutions. It is beneficial because it allows for innovative solutions that can yield substantial quality improvements. A notable feature here is the application of design of experiments (DOE), which helps in systematically testing and refining ideas. Nonetheless, a challenge could arise from resistance to changing established processes, particularly if proposed changes don’t seem to address the pressing problems.
Control Phase
Finally, the Control Phase is where implemented changes are monitored to ensure sustainability. This phase's key characteristic is the establishment of control systems and monitoring processes to prevent reverting to old habits. This aspect is vital for sustaining improvements over time. The unique feature is the development of control plans that specify how new procedures will be enforced and tracked. A potential disadvantage here might be the ongoing costs associated with monitoring systems, which some organizations may overlook when calculating the benefits of Six Sigma.
DMADV Methodology
While DMAIC focuses on improving existing processes, DMADV is geared towards creating new ones, with its phases being Define, Measure, Analyze, Design, and Verify. Understanding this methodology is crucial for scenarios where innovation is the goal rather than mere improvement.
Define Phase
In DMADV, the first Define Phase also centers on defining project goals. However, this is particularly tied to customer needs and project deliverables. The distinguishing trait is the collaborative approach involving cross-functional teams to ascertain comprehensive objectives. It is a beneficial method for ensuring alignment on project aims. Unique features include clearly demarcating customer requirements and success metrics from the outset, a tactic that clarifies expectations. A downside here, similar to DMAIC, is that the initial phase can consume significant resources and time.
Measure Phase
During the Measure Phase, DMADV focuses heavily on verifying customer requirements and measuring how well existing processes fulfill these before designing new solutions. This phase is vital as it ensures that any new design will meet customer expectations. It benefits organizations by reducing the likelihood of redesigning a product based on erroneous assumptions. The emphasis on customer metrics as a basis for design choices is a unique aspect. However, if customer needs are inaccurately assessed, the entire new design process can falter.
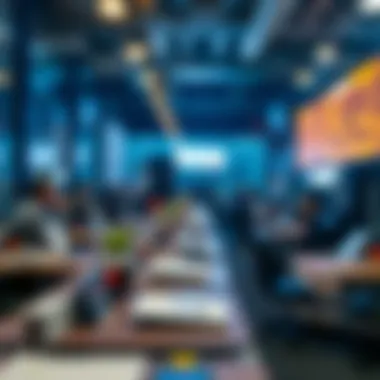
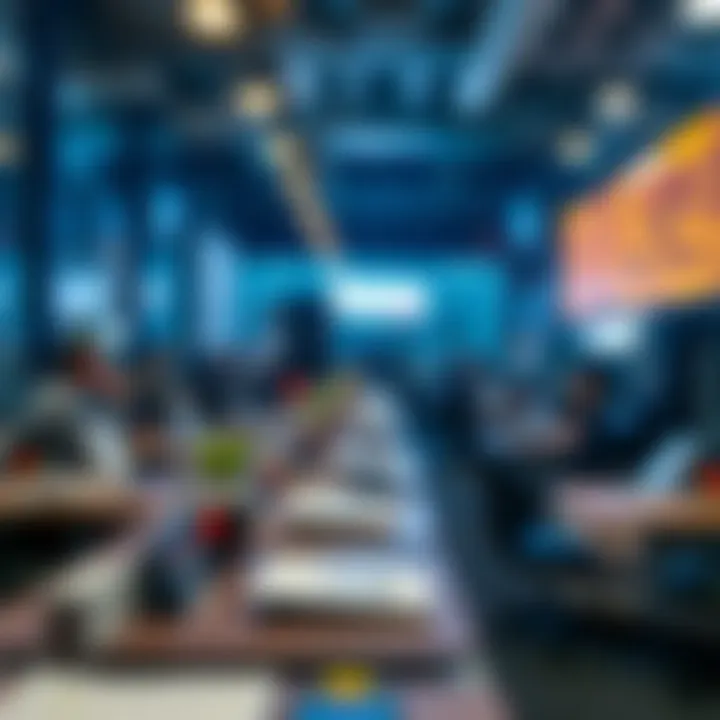
Analyze Phase
In the Analyze Phase, data is scrutinized to understand gaps between current performance and desired metrics. This phase is notable for using advanced analytical tools, often including simulations or modeling techniques to visualize outcomes. It serves as a crucial tool in predicting the success of future solutions before implementation. Yet, depending on the tools and data utilized, there might be complexity involved in analysis, potentially hindering effective conclusions.
Design Phase
Taking up the Design Phase, teams create the new process or product based on in-depth analysis. This is characterized by iterative processes, allowing for adjustments and refinements. The benefit is heightened innovation due to the lack of existing process constraints; teams are free to explore possibilities. A unique element is that concepts may undergo multiple design iterations before a final version is selected. The downside, however, might include delays driven by the iterative nature of the design, which could feel laborious to teams eager for swift outcomes.
Verify Phase
Concluding with the Verify Phase, the goal is to confirm that the designs meet all requirements and perform as intended. It emphasizes testing and validating prototypes to ensure that the design effectively meets predefined customer criteria. The emphasis on verification ensures a higher likelihood of success upon launch. A distinct feature is conducting pilot runs before full-scale production. On the downside, this phase may require additional resources for extensive testing budgets, which some organizations might find challenging to allocate.
Roles in Six Sigma
Understanding the various roles within the Six Sigma framework is crucial for its successful implementation and achieving continuous improvement. Each role, often referred to as a "belt" in Six Sigma terminology, represents different levels of expertise and responsibility. The clear definition of these roles ensures that everyone within an organization knows their specific contributions to quality management. This clarity not only enhances teamwork but also streamlines processes aimed at eliminating defects and fostering efficiency in operations.
The classification of roles into various belts enables organizations to deploy their staff effectively, ensuring that projects have the right level of expertise. It’s like having the right tools for the job; the distinction between White, Yellow, Green, Black, and Master Black belts streamlines the path toward achieving operational excellence.
Six Sigma Belts Explained
White Belt
The White Belt serves as the foundation of the Six Sigma roles. Individuals holding this title are typically introduced to basic Six Sigma concepts and tools. Even though the role is not highly specialized, it plays an important part in supporting the implementation of Six Sigma at a grassroots level.
The key characteristic of a White Belt is their broad awareness of the Six Sigma methodology, making them a valuable asset to the team. They often assist in data collection and process mapping, providing crucial support in projects.
While the White Belt does not lead projects, they are effective team members who understand the importance of quality improvements in operations. The unique feature of this role is its accessibility; nearly any employee can take on the White Belt responsibilities, allowing for a widespread understanding of quality practices throughout an organization.
Yellow Belt
Moving up the ladder, the Yellow Belt offers a deeper dive into Six Sigma principles. Yellow Belts possess a more robust understanding of the tools and techniques, making them instrumental in Kaizen events and other improvement initiatives.
The hallmark of a Yellow Belt is their ability to contribute actively to project teams while under the direction of Green or Black Belts. This often includes supporting data collection and analysis.
One advantage of the Yellow Belt role is its relatively low barrier to entry compared to higher belts. The training required is less intense, making it an attractive option for those looking to enhance their skills without committing to the extensive training higher belts require.
Green Belt
The Green Belt role takes on a more significant responsibility in project management and data analysis compared to the previous belts. Green Belts are often working professionals who lead smaller scale projects while collaborating with Black Belts on more complex initiatives.
A crucial characteristic of a Green Belt is their competency in utilizing Six Sigma tools to analyze and improve processes. Their engagement enables organizations to implement Six Sigma practices across different levels, driving impactful outcomes.
What sets Green Belts apart is their dual function; they operate within their functional area while also participating in Six Sigma projects, leading to multiple benefits. This cross-pollination of knowledge helps in embedding a culture of quality awareness.
Black Belt
Black Belts represent a high level of expertise in Six Sigma principles. Their primary responsibility is for leading meaningful projects that require substantial change and delivering significant improvements in processes. Black Belts are often full-time practitioners who spend their days honing their mastery of Six Sigma methodologies.
A defining trait of a Black Belt is their ability to mentor and train others. They orchestrate the efforts of project teams, driving necessary changes and ensuring alignment with organizational goals.
While a Black Belt can be a demanding and high-stakes role, the results they produce are often transformative. By leading major initiatives, they positively impact both efficiency and cost-effectiveness.
Master Black Belt
At the pinnacle of the Six Sigma hierarchy is the Master Black Belt. This individual is not just an expert in the methodologies but also acts as a strategic leader within the organization, driving the Six Sigma philosophy across various functions.
They possess advanced skills in statistical analysis, project management, and change management, ensuring that Six Sigma practices are integrated into the organizational fabric. The key characteristic here is their leadership in mentorship and training of Black and Green Belts, fostering a culture of excellence.
The unique advantage of a Master Black Belt is their ability to guide strategic decisions based on their extensive knowledge of Six Sigma, influencing higher-level business strategies. Such depth of expertise ensures that Six Sigma initiatives align with overall organizational objectives.
Responsibilities of Each Role
Each role defined within the Six Sigma framework carries its distinctive set of responsibilities, requiring team members to play their parts effectively. A well-orchestrated team, with each belt operating within its defined parameters, fosters a collaborative environment focused on operational excellence.
- White Belt: Participates in improvement projects, collects data, and provides essential support.
- Yellow Belt: Assists project teams, contributes to team meetings, and undertakes minor data analysis.
- Green Belt: Leads projects, manages teams, and drives key improvements under guidance of Black Belts.
- Black Belt: Guides project teams, operates complex projects, and is accountable for major operational improvements.
- Master Black Belt: Mentors others, guides training programs, and connects Six Sigma initiatives with broader organizational strategy.
Understanding these roles helps clarify how individuals contribute to the overarching goals of Six Sigma practices. Their collective efforts ensure a consistent path toward achieving quality improvements, leading to greater operational efficiency and effectiveness in an increasingly competitive landscape.
Challenges in Implementing Six Sigma
Implementing Six Sigma can transform processes, but it's not without its hitches. Embracing this quality management system often encounters a handful of challenges that can throw a wrench in the works for many organizations. Understanding these challenges is critical as companies strategize their Six Sigma initiatives. Recognizing pitfalls allows stakeholders to foresee issues and establish solid plans to mitigate them, ensuring the success of their commitment to quality improvement.
Resistance to Change
One of the most formidable adversaries organizations face is resistance to change. Change can be unsettling; it disturbs the status quo that many employees have grown accustomed to. When introducing Six Sigma, it is common for team members to exhibit skepticism or outright opposition. They may feel their jobs are at stake or question the need for new processes.
Addressing this resistance requires tactical communication. It’s important to foster an open dialogue about the benefits of Six Sigma. Management should demonstrate how these changes can not only enhance operational efficiency but also create a more satisfying work environment. Engaging employees early on can lead to a smoother transition. Consider using testimonials from others who've successfully implemented Six Sigma to showcase potential improvements.
"The greatest danger in times of turbulence is not the turbulence; it is to act with yesterday's logic."
– Peter Drucker
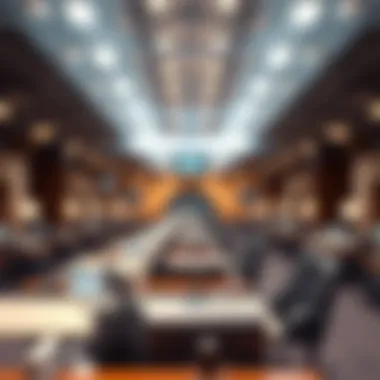
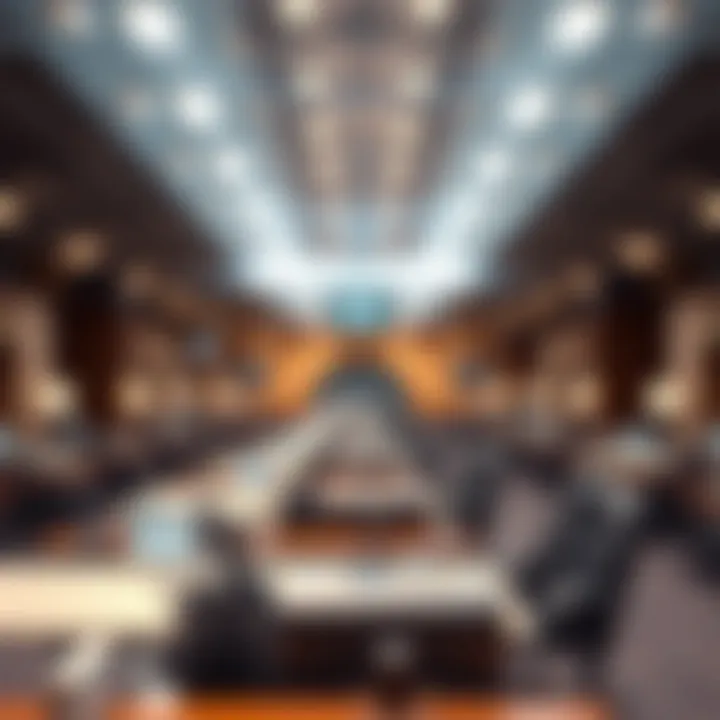
Resource Allocation
Resource allocation poses another significant challenge. Quality initiatives demand time, financial backing, and talent. Organizations might find it difficult to prioritize Six Sigma amidst competing demands. A lack of adequate resources can lead to half-hearted attempts at implementation, culminating in failure. Therefore, strategic planning is key.
Here are a few aspects to consider when allocating resources:
- Financial Resources: Ensure budgetary alignment with Six Sigma goals. Adequate funding facilitates training, workshops, and potential external consulting.
- Human Resources: Having trained personnel is crucial. Lacking a skilled team can hinder efforts. Organizations often need to invest in proper training for existing employees or hire new talent with experience in Six Sigma methodologies.
Companies need to assess their current workload and strategize accordingly. Investing time and resources before jumping in can make a world of difference when rolling out Six Sigma.
Training and Skill Development
Training and skill development cannot be overlooked. Even with the best intentions, a monumental failure can occur if employees are inadequately trained. Six Sigma methodologies require a fundamental shift in how employees view quality management. Without sufficient knowledge, understanding becomes superficial.
Organizations should consider these key elements:
- Comprehensive Training Programs: Conduct regular sessions that not only cover the basics but also delve into practical applications of Six Sigma. This empowers employees to use these techniques confidently in their daily tasks.
- Mentorship and Support: Pairing more experienced Six Sigma practitioners with novices can enhance learning and foster collaboration.
- Assessment and Feedback: Implement frequent assessments to gauge understanding and provide constructive feedback. This encourages continuous improvement and underscores the importance of mastery in Six Sigma methodologies.
These initiatives will embed Six Sigma principles into the company culture, transitioning from mere knowledge to genuine application in organizational processes.
Six Sigma in Various Industries
The application of Six Sigma has permeated multiple sectors, offering unique benefits tailored to the challenges specific to each industry. Understanding Six Sigma's nuances is crucial, given its prominent role in driving efficiencies, boosting quality, and enhancing customer satisfaction. As organizations strive to remain competitive, the methodologies underpinning Six Sigma find relevance across diverse fields. Below, we delve into how various industries have embraced this quality management system, showcasing distinct elements and outcomes that set them apart.
Manufacturing Sector
In manufacturing, Six Sigma has revolutionized processes, aiming primarily to reduce defects and improve productivity. The environment is inherently conducive to the application of DMAIC methodology, where precise measurement and analytics are paramount. For instance, a company producing automotive parts may implement Six Sigma to identify inefficiencies in their assembly line. By utilizing tools like process mapping and statistical analysis, they can pinpoint areas where defects arise, optimize workflows, and thus minimize waste.
"Quality is not an act; it is a habit." — Aristotle
Adopting Six Sigma in manufacturing can result in significant cost savings and enhanced operational capacity. The emphasis on data-driven decisions allows manufacturers to maintain strict quality controls, leading to higher customer satisfaction. Furthermore, companies often witness reduced cycle times, translating into faster delivery and improved competitive edge.
Healthcare Applications
Healthcare systems have increasingly recognized the need for operational excellence, making Six Sigma a critical component in their strategic plans. The stakes are high, where errors aren't just costly but can also endanger lives. Hospitals employing Six Sigma techniques strive to enhance patient care quality while optimizing resource allocation. A facility may adopt DMADV to reengineer service delivery processes, ensuring that patient safety and satisfaction are paramount.
For example, a hospital might track the time taken from patient admission to treatment. By analyzing this metric, healthcare providers can develop better protocols that ensure timely care. Benefits have been seen across reducing wait times in emergency departments, enhancing surgical outcomes, and even improving patient discharge processes—all essential for operational success.
Finance and Banking
In the finance sector, precision and efficiency are sacred. Here, Six Sigma assists institutions in refining processes, minimizing errors in transactions, and enhancing compliance mechanisms. For instance, a bank utilizing methodology like DMAIC can address customer service complaints systematically, which often lead to larger operational disruptions. By focusing on data quality and customer feedback, financial institutions can enhance service strategies, reduce response times, and ultimately retain clients better.
Moreover, financial organizations are leveraging Six Sigma to bolster risk management. By identifying nonconformance in process flows or analyzing loan approval stages, institutions minimize exposure to risk and streamline operations, leading to increased trust from clients.
Service Industry Innovations
The service industry, quite dynamic in nature, has shown that Six Sigma can lead to significant improvements in various aspects, from customer experience to process management. Organizations ranging from hospitality to retail utilize Six Sigma to streamline operations, making them more responsive to customer needs. For instance, a hotel chain may undertake Six Sigma projects to assess guest feedback and operational delays.
By measuring consistency in service delivery, staff productivity, and customer satisfaction levels, they can refine their training protocols and enhance guest interactions. Such systematic feedback loops promote a culture of continuous improvement, ensuring the service aligns with customer expectations.
Additional benefits include improving employee engagement—where employees are actively involved in identifying problems and crafting solutions—making the workplace feel more invested in success.
Success Stories and Case Studies
Examining success stories and case studies within the Six Sigma framework provides invaluable insights that enhance the overall understanding of its methodologies and outcomes. These narratives offer real-world examples of how organizations have successfully implemented Six Sigma principles, showcasing the various paths to achieve operational excellence. By exploring these stories, investors, financial advisors, and analysts can recognize the tangible benefits of embracing such practices and may even glean strategic lessons applicable to their own contexts.
Notable Case Studies
General Electric
General Electric (GE) serves as a prominent example in the realm of Six Sigma adoption. GE's commitment to quality management has been clear, especially under the leadership of Jack Welch. The unique aspect of GE’s approach lies in its integration of Six Sigma with its business strategy, resulting in improvements in product quality and process efficiencies. GE’s notable emphasis on data-driven decision-making exemplifies a critical characteristic of a successful Six Sigma implementation.
One of the striking features of this case is how GE used Six Sigma principles not just to solve problems, but to foster a culture of continual improvement. This aspect has made GE's methodology a popular choice when examining Six Sigma applications. The advantages include measurable enhancements in productivity and profitability, while a potential disadvantage could be the initial resistance from employees who might perceive such a rigorous methodological change as overwhelming.
Motorola
Motorola is often credited with the birth of the Six Sigma concept back in the 1980s. One specific aspect of Motorola's influence is its focus on reducing defects in manufacturing processes, which led to significant cost savings and efficiency gains. Motorola’s success story underscores a key characteristic: their commitment to quality at every level, starting from the top management down to the floor workers.
Motorola’s unique feature is its pioneering role in defining the metrics for quality, notably the term "Six Sigma" itself, which indicates a goal of only 3.4 defects per million opportunities. The advantage here is evident; by setting such high standards, Motorola positioned itself as a leader in quality and innovation. However, the challenge lies in sustaining such high expectations across all operations, which may be daunting for some companies aiming to replicate this model.
AlliedSignal
Another noteworthy case is AlliedSignal, which utilized Six Sigma to improve its processes and products significantly. Their approach centered on leveraging Six Sigma not just for quality control, but as a means of fostering innovation. This dual focus on improvement and creative thinking is what sets AlliedSignal apart in the discussion of Six Sigma applications.
The defining characteristic of AlliedSignal is its ability to drive change across its operations while maintaining employee engagement. This case is beneficial for this article as it exemplifies how a firm can simultaneously improve performance and employee morale. A unique feature here is their emphasis on teamwork, which can lead to more sustainable gains. On the flip side, the challenge is managing varying levels of commitment from team members, especially when adapting to a culture of change.
Key Takeaways from Case Studies
The case studies discussed provide several critical insights:
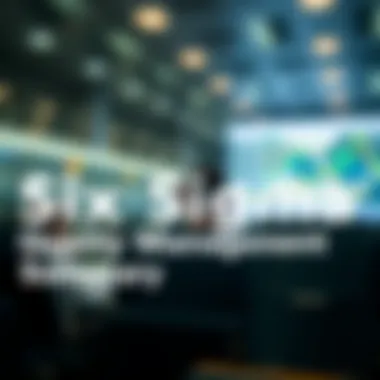
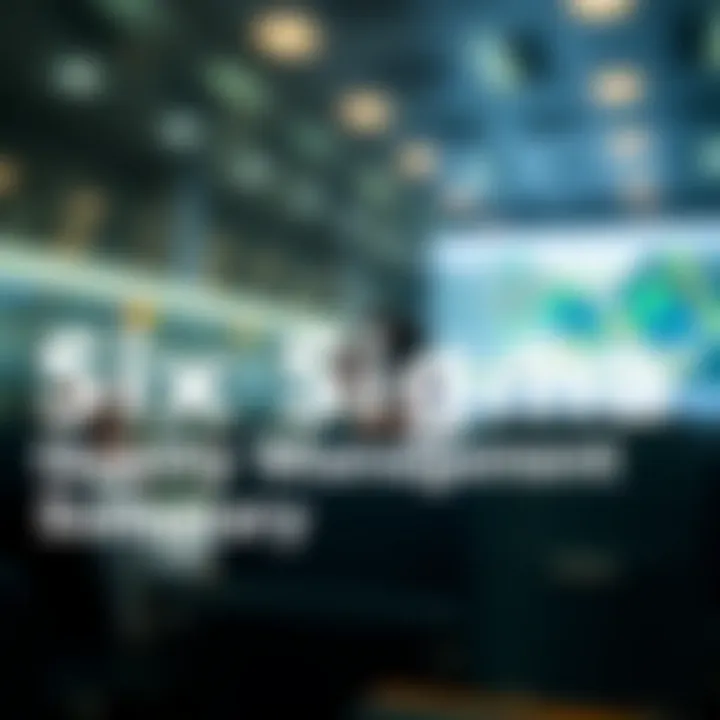
- Data-Driven Decisions: Successful Six Sigma implementations rely heavily on data analysis, illustrating the importance of robust measurement.
- Leadership and Culture: Strong commitment from leadership is crucial to cultivating an organizational culture that embraces quality management.
- Continuous Improvement: Each of these companies showcases the necessity of ongoing evaluation and adaptation to new challenges and opportunities.
- Employee Engagement: Maintaining high morale and team cohesion is essential, as it motivates individuals to participate actively in process improvements.
Understanding these success stories arms financial professionals and investors with the knowledge to advocate for Six Sigma methodologies in their organizations, demonstrating proven benefits derived from leading companies.
For further insights, you may explore resources like Wikipedia, Britannica, and industry analyses available on Reddit or other academic sources.
Best Practices for Six Sigma Implementation
Implementing Six Sigma is no small feat. It requires a clear understanding of methodologies, strong leadership, and a commitment to continuous improvement. This section emphasizes the best practices that can help organizations successfully integrate Six Sigma into their operational framework.
• Define Clear Objectives: Before embarking on a Six Sigma journey, it’s vital that a company identifies what it aims to achieve. Whether it’s reducing defects, improving customer satisfaction, or increasing efficiency, aligning the Six Sigma project with business goals can strengthen the initiative’s foundation.
• Engage Employees at All Levels: For Six Sigma to take root, it needs to be embraced by the entire organization. That means involving employees right from the get-go. When frontline staff understand the benefits and methodologies of Six Sigma, they are more likely to contribute actively to its success. This engagement also fosters a culture of quality, where everyone takes ownership of their roles in the process.
"Effective leadership in Six Sigma implementation is not just top-down; it garners grassroots support."
• Invest in Training and Certification: As the Six Sigma framework often employs specialized terminology and processes, training is essential. Providing employees with training that aligns with their specific roles (like White Belt, Green Belt, etc.) ensures that everyone is equipped to lead and support initiatives. Investing in education leads to better results and more robust employee morale.
• Utilize Data-Driven Decision Making: Six Sigma stands on the pillars of data and analysis. Organizations should foster a culture where decisions are backed by data, not just instinct or experience. This method of decision-making significantly reduces waste and error, leading to improved quality outputs.
• Establish a Pilot Program: Before a full rollout, implementing a pilot project can provide valuable insights and identify hurdles. Managing a smaller-scale Six Sigma project allows an organization to gauge the effectiveness and adapt methodologies accordingly, minimizing risk on a larger scale.
• Foster Continuous Improvement: Six Sigma isn't just about achieving once and resting on your laurels. Organizations must cultivate an environment of ongoing enhancement. Regularly revisiting processes and the effectiveness of the strategies ensures that they remain relevant and effective in changing market conditions.
Establishing Leadership Commitment
Leadership commitment is the bedrock of any successful Six Sigma implementation. Without strong support from those in senior positions, initiatives can quickly lose momentum. Leaders need to communicate the vision of Six Sigma clearly and demonstrate their commitment through actions. They should be actively involved in projects, celebrate successes, and help overcome challenges that may arise.
Leaders must also ensure that resources are allocated adequately to Six Sigma projects and that those involved have the authority to make decisions. When leadership is visibly committed, it builds trust within teams and reinforces the importance of continuous improvement across the organization.
Continuous Monitoring and Adaptation
Monitoring and adaptation are crucial in maintaining the efficacy of Six Sigma practices. Once processes are implemented, organizations cannot afford to be complacent. Regularly measuring outcomes against the standards set at the beginning allows for real-time feedback. Metrics such as defect rates, customer satisfaction scores, and operational efficiency need ongoing review.
Adapting to the findings from monitoring ensures that any issues are addressed promptly and that improvements can be continually implemented. This iterative approach not only fuels growth but also ensures that the organization remains agile in a dynamic market. By embracing adaptation, businesses can better respond to fluctuations in consumer needs or shifts within the industry overall.
By adopting these best practices, organizations can lay a solid foundation for Six Sigma, harnessing its full potential for operational excellence.
Linking Six Sigma with Operational Excellence
Linking Six Sigma with operational excellence is crucial because it helps organizations not only achieve but also sustain high levels of performance. When businesses harness Six Sigma principles, they're actively engaging in a systematic approach to enhance both processes and outcomes. This connection facilitates a culture of continuous improvement where every employee is encouraged to contribute to the overall effectiveness of the organization.
Such operational synergy plays a significant role in high-stakes environments, where small inefficiencies can lead to massive financial losses. In a world where quality is king, and competition is fierce, aligning Six Sigma practices with operational excellence can lead to remarkable improvements in productivity, customer satisfaction, and bottom line success.
In this context, it's essential to understand what operational excellence entails and how Six Sigma methodologies can serve as a structured approach to attain this state.
Defining Operational Excellence
Operational excellence refers to the execution of the business strategy more consistently and reliably than the competition. It is about an organization's ability to deliver products or services efficiently while maintaining or improving quality. To achieve operational excellence, companies often focus on various factors such as:
- Process improvement: Optimizing existing processes to eliminate waste and reduce variations.
- Customer focus: Prioritizing the needs and preferences of customers to enhance their experience.
- Agility and adaptability: Ensuring that organizational structures are nimble, with the capacity to respond quickly and effectively to market changes.
- Employee engagement: Fostering a workplace culture that empowers employees, encourages collaboration, and values their input.
Operational excellence is not a one-time effort; it's a continuous journey requiring commitment from all levels, especially leadership.
Integrative Strategies
To truly link Six Sigma with operational excellence, organizations must employ integrative strategies that meld the best practices of both realms.
- Cross-Functional Teams: Establishing teams that bring together diverse roles and viewpoints can encourage innovative problem-solving and enhance collaboration across departments.
- Data-Driven Decision Making: Leveraging data analytics can help organizations identify process bottlenecks, measure performance, and make informed strategic decisions that align with both Six Sigma and operational excellence goals.
- Training and Development Programs: Continuous learning is essential for both Six Sigma practitioners and other employees. By investing in training programs, firms can better equip their staff with the necessary skills to drive quality improvements throughout the organization.
- Cultural Alignment: The journey to operational excellence must be embedded into the company culture. Establishing shared values, focused on quality and continuous improvement, can effectively motivate and engage employees in this pursuit.
- Regular Review and Feedback: Creating a system of periodic reviews and gathering feedback from employees at all levels can help identify areas for improvement and ensure alignments with operational excellence strategies.
A seamless integration of Six Sigma and operational excellence principles fosters a mindset of innovation and continuous improvement, propelling organizations towards their strategic goals.
Ultimately, linking Six Sigma methodologies with operational excellence is not just about increasing efficiency; it's about fostering a holistic approach to quality management that infuses itself into every part of the organization.
Future Trends in Six Sigma
As industries continue to evolve, so does the need for robust quality management systems. The future of Six Sigma aligns closely with these changes, presenting a unique opportunity for organizations aiming to enhance operational efficiencies. Highlighting future trends in Six Sigma is essential, as it not only keeps businesses abreast of crucial developments but also sheds light on how they can leverage these advancements for significant gains.
In the upcoming years, we anticipate two prominent trends shaping the landscape of Six Sigma: the adoption of technology and the increasing emphasis on sustainability. Organizations adopting these trends can expect improved quality, reduced waste, and enhanced customer satisfaction.
Adoption of Technology in Six Sigma
The rise of digital technology is undeniably changing the way organizations implement Six Sigma methodologies. From the integration of big data analytics to the utilization of artificial intelligence, technology enhances the precision with which data is collected and analyzed. Some key elements include:
- Data Analytics: The ability to analyze vast data sets allows organizations to identify patterns and insights that were previously unattainable. This can lead to more accurate predictions and better decision-making.
- Automation: Automated processes reduce human error and enhance efficiency. Tools like robotic process automation (RPA) streamline repetitive tasks, allowing employees to focus on value-added activities.
- Machine Learning: Machine learning algorithms can improve the DMAIC and DMADV processes by enabling predictive analysis. This can lead to more effective solutions tailored to specific issues within the company.
Adopting these technological trends translates to a more data-driven approach, which enhances the overall execution of Six Sigma. Companies looking to remain competitive must invest in their technological infrastructure to fully realize Six Sigma’s potential.
Sustainability and Six Sigma
With increasing global awareness about environmental issues, sustainability is becoming a hot topic among organizations. Six Sigma incorporates sustainability by emphasizing waste reduction and resource efficiency. Here are some considerations:
- Eco-Friendly Practices: Integrating eco-friendly practices into the Six Sigma framework can lead to reduced carbon footprints. Through techniques like value stream mapping, organizations can identify areas where they can minimize waste.
- Social Responsibility: Companies that adopt sustainable practices tend to build better reputations. An organization committed to sustainable practices can create a positive image, attracting customers who prefer to support eco-conscious businesses.
- Regulatory Compliance: As sustainability regulations become more stringent, maintaining compliance becomes crucial. Implementing Six Sigma promotes adherence to these regulations through systematic quality improvement processes.
Organizations must prepare now for future trends in Six Sigma to reap the benefits of enhanced operational efficiencies and competitive advantages.